Drying process of flash dryer
The heat exchange in the dryer is mainly based on the heat exchange between the gas stream and the particles, the wall and the particles. The essence of the drying process is the diffusion process of moisture. It is carried out by external diffusion and internal diffusion. Out-diffusion is the process by which the surface moisture of a particle diffuses from the surface to the surrounding medium in the form of steam. Internal diffusion is the process by which moisture moves inside the particles.
The flash dryer adopts high-speed hot air tangential direction to enter the cylinder. Due to the spiral motion of the airflow in the cylinder, on the one hand, the temperature of the medium around the particles is lowered, and the medium flow rate and temperature are increased, which greatly increases the speed of out-diffusion. . On the other hand, the high-temperature airflow impacts the particles or small wet materials located at the lower part of the cylinder at a high speed, and at the same time, the stirring action of the stirring blades in the cylinder causes the particles to be broken, the particle size is reduced, and the length of the internal capillary is also reduced, and the inner diameter is strengthened. The effect of diffusion reduces the resistance to internal diffusion. Most of these particles are repeatedly broken in the cycle of high temperature and high agitation intensity in the lower part of the cylinder. Eliminating material agglomeration is also a powerful measure to promote internal diffusion, which enhances the evaporation of particulate water.
The flow of particles and hot gas flows: there are both convection and cocurrent flow in the lower part of the cylinder, and convection and parallel flow are repeated for the coarse material. For fine-grained materials, it is parallel with the hot gas flow, so the drying process can be completed in an instant. Drying of the granules is actually a hot air drying with high temperature and low humidity. These particles are mainly adsorbed by water and filled in the interstices of the particles. The conditions of high temperature and low humidity are adopted, and the heat conduction of the whole particles is slow, causing local stress concentration, dry cracking, crushing, dispersing and accelerating the drying process.
After the material enters the dryer, the hot gas first transfers heat to the surface of the particle, causing evaporation of the surface moisture. The moisture inside the material particles diffuses to the surface and spreads to the outside. After the Zui, the entire particle is dried. If the material does not undergo a chemical reaction during the drying process, the moisture content, temperature and drying rate of the material can be divided into the following stages as the drying time changes:
1. Speed ​​up drying stage. The particles are placed in a heat transfer medium with a relatively high temperature and a relative humidity of less than 100%. In a short period of time, the surface is heated to the wet bulb temperature of the drying medium, the evaporation rate of water is increased rapidly, and the heat and evaporation of the particles after a certain time. The amount of heat consumed by the water is equal and reaches equilibrium. The time in this phase is very short, the amount of water discharged is not large, and then enters the constant speed stage.
2. Constant speed drying stage. In some stages, the water evaporated from the surface of the particles is continuously replenished from the inside to the surface of the particles, and the surface is always kept wet. At this time, the drying rate remains unchanged, and the surface temperature of the particles remains unchanged. The evaporation rate is related to the difference in water vapor concentration and temperature difference between the surface of the particles and the surrounding medium. The larger the difference, the greater the drying speed. In addition, the drying rate is also related to the air velocity on the surface of the particles. There is always a layer of air film that does not flow on the surface of the particles, thereby increasing the velocity of the airflow on the surface of the particles, so that the air film is thinned and the drying rate can be increased. Drying continues for a certain period of time, the internal moisture diffusion rate of the particles begins to be less than the surface evaporation rate, and the moisture in the particles cannot completely wet the surface to maintain the evaporation of the surface, and then enters the next drying stage.
3. Cooling and drying stage. After the water evaporates to a certain amount, the internal moisture of the particles is insufficient to completely wet the surface, the wet surface is gradually reduced, and the drying rate is gradually decreased. In this stage, the evaporation rate and heat consumption are greatly reduced, and the surface temperature of the particles is higher than the wet bulb temperature of the medium. Gradually increasing, the temperature difference from the carrier decreases until it is close or the same.
4. The balance phase. At this time, the moisture moisture and evaporation of the surface of the particles reach equilibrium, and the drying rate is zero.
The moisture in the granules is the final moisture of the dry zui and should generally not be lower than the equilibrium moisture at the time of storage. Rotary flash dryers have a very short residence time in the dryer due to the small particle size after drying, usually 1-3 s. Therefore, the drying temperature of the particles in the constant-speed drying stage, the temperature of the surface is the wet bulb temperature of the drying medium. The rotary flash dryer is used to make the material uniform in size, which is beneficial to ensure product quality.
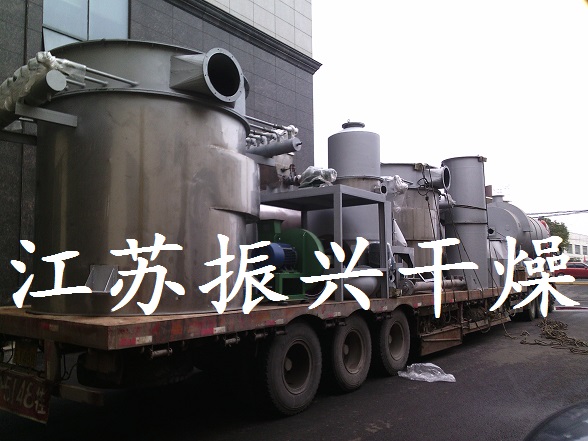
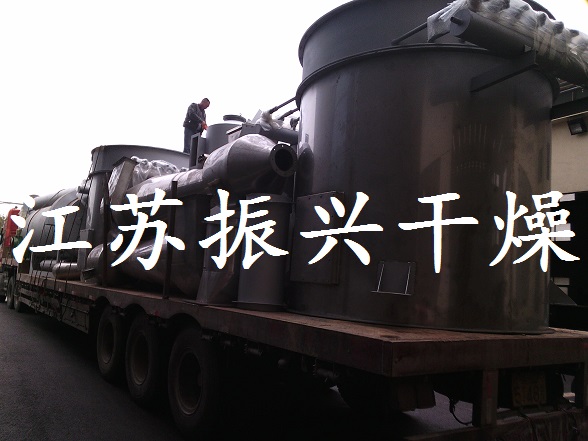
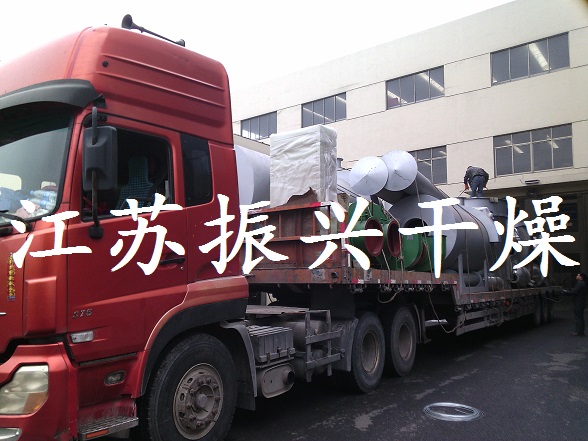
GMP ATS Injection, Tetanus Antitoxin, Tetanus Toxoid ,Tetanus Antitoxin Injection, Antitetanus, Refined Tetanus Antitoxinsupplier in China
Tetanus Antitoxin,Tetanus Toxoid,Tetanus Antitoxin Injection,Antitetanus&Refined Tetanus Antitoxin
FOSHAN PHARMA CO., LTD. , https://www.foshanmedicine.com