As an important method of sterilization and particle removal, microfiltration membrane filtration has been widely used in sample processing of pharmaceutical, particle detection and analytical instruments. As the most common needle filter in the laboratory, in addition to the need for dissolution testing, chemical compatibility testing, integrity testing should also be done.
Filter integrity is an important indicator in filtration products. Whether a filtration system can guarantee its integrity before and after filtration is an important parameter to measure the quality of a filtration product. For filtration processes, especially for sterilization-grade filtration, integrity testing is a necessary means to ensure the safety and reliability of filtration and to avoid unnecessary waste in the work, including time, effort, and filtration of samples. Through the integrity test, you can ensure that:
1. The integrity of the filter itself, the tightness of the filtration system;
2. The filter membrane is not damaged, no flaws, and the selected filter membrane meets the filtration requirements;
3. The filter is installed in the process and the operation is correct;
4. The installed filter conforms to the standards provided by the manufacturer.
Integrity testing methods fall into two broad categories, destructive and non-destructive. The so-called destructive test refers to the bacterial challenge test, which is the fundamental method to prove that the filter can meet the demanding sterilizing grade filter standard. In the bacterial challenge test, a certain number of samples should be taken from each batch of products according to statistical principles, and the Pseudomonas aeruginosa solution should be used to perform the bacterial challenge test according to the standard test method. Usually, the producer of the filter material will perform such destructive tests to check whether the quality of the product is acceptable.
Non-destructive testing methods mainly include bubble point testing (also known as starting point testing) and diffusion testing. For users of small filter products, the bubble point test is a simple and easy test method. It can pass the bubble point test to check the performance of the selected filter product and determine whether the filter result is valid or not.
Briefly introduce the basic principles of bubble point testing:
The bubble point test is based on a capillary model. The structure of the membrane is filled with microporous channels, which are the basic units of filtration. These microporous flow channels are like many "capillaries". When the filter membrane is completely wetted by the wetting liquid, the liquid is retained by the surface tension and remains inside the "capillary". If you want to squeeze the liquid out of the membrane hole, you need it. In addition to a gas pressure to overcome the surface tension, the minimum pressure required to completely extrude the liquid in the pores of the membrane is the bubble point value of the membrane, which is often referred to as the bubble point. The test method based on this principle is the bubble point test method. This is also the most widely used non-destructive integrity test method. The following is the formula for calculating the bubble point value:
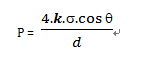
Where P = bubble point pressure; d = aperture; k = shape correction factor; q = liquid-solid contact angle; s = surface tension
The bubble point value is directly related to the filter aperture. There are many micropores on the filter membrane, and the bubble point value of each pore is not necessarily the same, and the bubble point value of the membrane refers to the bubble point value of the largest membrane pore in the membrane, that is, the bubble of the largest diameter membrane pore. Point (where the liquid is most easily extruded to form a channel). When the bubble point is reached, the liquid in at least one of the well-wet membranes is squeezed out to form a gas passage, so that the gas is quickly blown through the hole to the downstream of the membrane to form a continuous stable bubble. From the sudden change in the downstream gas flow rate, it can be judged whether or not the bubble point is reached. If it is a large-area filter, the judgment of the bubble point is easily affected due to the large diffusion flow, so the diffusion flow test is recommended for the manual test of the large-area filter; for the small-area filter, the bubble point and the filter aperture can be directly related. The use of bubble point test is fast and convenient.
The bubble point value is a characteristic index of a filter medium. For a specific material, a filter material of a specific pore size, the bubble point value is theoretically a fixed value. Due to measurement errors and other factors, the measured value will appear in a fixed range. Usually, the filter manufacturer will indicate the minimum value of the bubble point value of a particular filter.
Needle filters are widely used by laboratory and analytical researchers in the life sciences for their simplicity and convenience. The seemingly simple small filter plays a key role in the experimental process, not only to ensure the smooth progress of subsequent experiments, to obtain accurate experimental data, but also to use it in chromatographic analysis to remove impurities, which can guarantee precision instruments. The service life reduces the risk of damage and thus maximizes cost savings.
Of course, there are some confusions in the use of the user. The filter membrane in the needle filter is sealed in it and cannot be seen. How can it be judged that a qualified filter is used in the filter? Is the filter sealed and not damaged? Indeed, if a filter of unqualified quality is used, the sample only passes up and down from the filter, and the impurities are not completely trapped by the filter in the filter, especially if the membrane is damaged. Or, if it is not completely sealed, the liquid will leak out of the gap, and subsequent experiments will not work properly, and will waste financial resources. In fact, these confusions are not difficult to eliminate. The quality of the needle filter can be easily identified by using the bubble point principle described above. Many of the industry's most well-known needle filter suppliers sell bubble point tester products for small filters. RephiLe also provides customers with a simple bubble point test widget that allows users to easily understand the quality of their filters.
The bubble point value measured by the bubble point tester is much lower than the characterization value of the filter film, which indicates that there is a big problem with this filter, which may be caused by the following aspects:
1. The filter membrane is damaged;
2. The filter has a leaky seal, and there is a gap between the filter and the filter;
3. The filtration system is leaking;
4. Filter material problem
Conversely, if the measured value is equal to or higher than the bubble point indicator given by the supplier, indicating that the filtration system is fully effective, the filtration effect is reliable.
In short, with the bubble point tester, you can easily choose a reliable needle filter product, so that your filtration has no worries.
Hunan Kangfutai Medical Devices Co., Ltd. , https://www.3kfut.com